Stopping Multiple Leaks At A Power Plant
HydraWrap® (Fiber Reinforced Polymer)
Market
Power
Challenge
A power plant in Kentucky had cracks forming on two aging concrete structures which were the cause of leaking. The first was a cooling tower basin’s wall. The wall required two points of repair. The other was a cooling water tunnel, specifically at a transition where a 70” I.D. steel pipe connected to a rectangular concrete tunnel.
Engineered Solution
Hydraulic cement would be used to fill the cracks and HydraWrap was to be applied over the cement for protection and strength. Finally, the repairs to the basin walls would be coated in a fast-drying urethane. The power plant chose HydraWrap as its installation is time-efficient.
Scope
The basin’s walls were first pressure washed and then the cracks had to be filled with hydraulic cement. Primer was then applied to the surface and four layers of HydraWrap were installed. Once the repair location was tack-free, a coat of fast-drying urethane was applied to provide UV protection.
The joint transition in the cooling tunnel had to be cleaned and leaks had to be drilled and then filled with hydraulic cement. Then this cement was used to contour and smooth out the abrupt transition. Once the prep work was completed, four layers of HydraWrap were installed. Once the HydraWrap had cured, a 70 ” diameter retaining band was installed on the 70” round side, on top of the edge of the HydraWrap. Eight flat bars were installed on the HydraWrap’s other side.
Both the basin wall and tunnel transition repairs were completed in 2 days each.
Solution
HydraWrap proved to be a time-efficient repair that provides the power plant with an economical long-term solution. The HydraWrap continues to function as designed years after the initial installation.
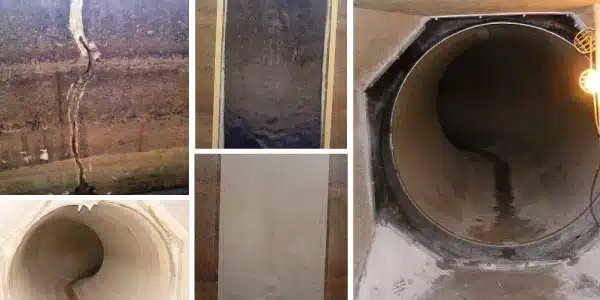
First let me commend HydraTech’s Work. We have had no further leakage since your repair. The tunnel was inspected last year and no issues were found.
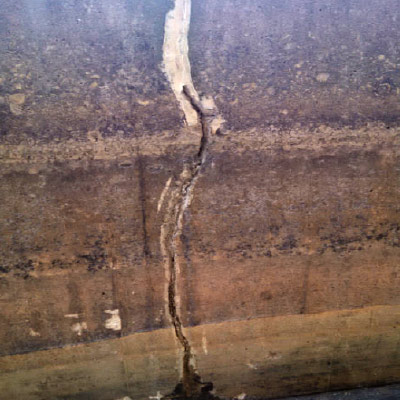

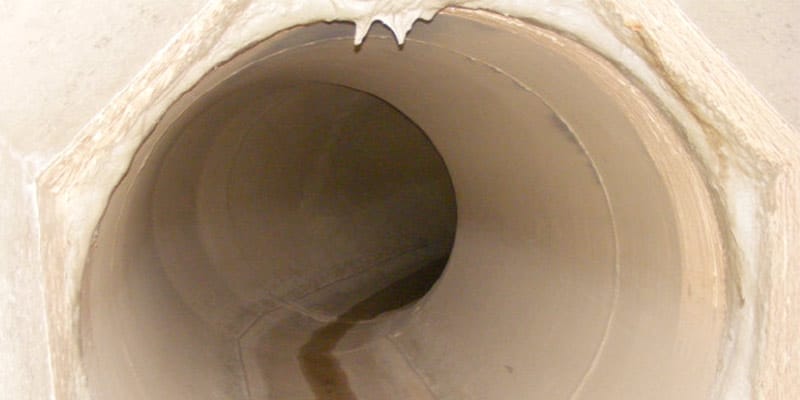
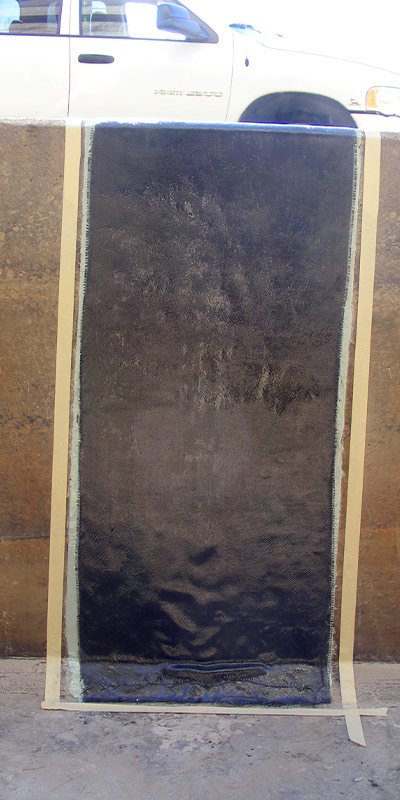
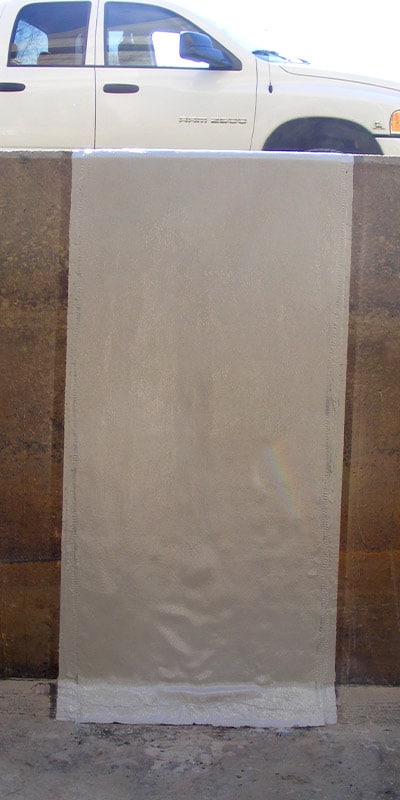
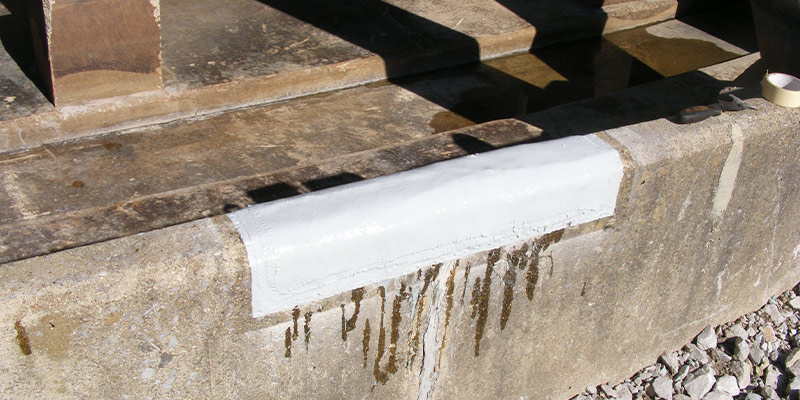
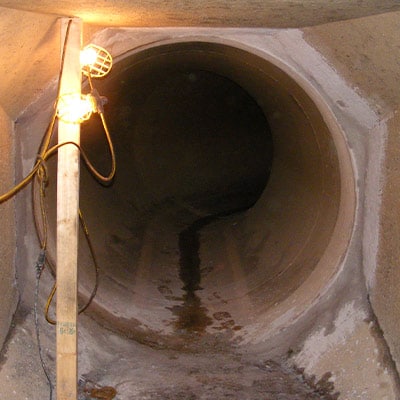
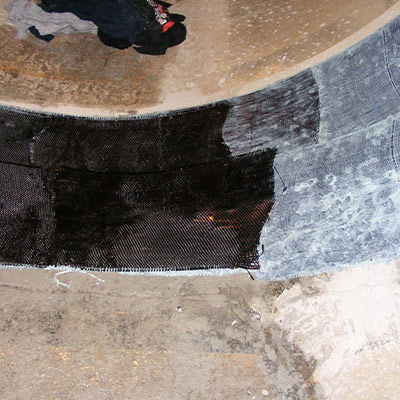
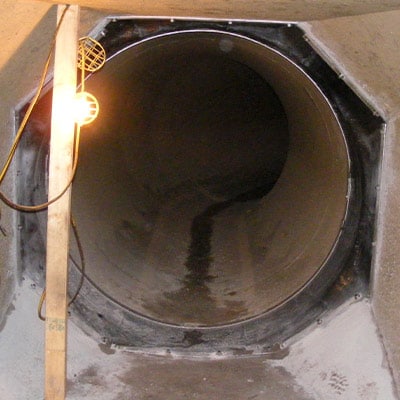
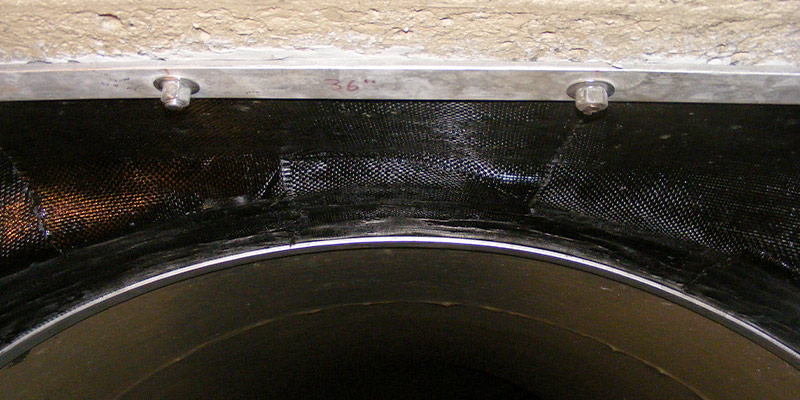
Explore HydraWrap
More Products
Case Studies
Explore HydraWrap
More Products
Case Studies
Explore HydraWrap
More Products
Case Studies
OUR PRODUCTS
Trenchless Repairs Custom Made
OUR INDUSTRIES
From Power to Water We Have It Covered
OUR RESOURCES
Technical Data Sheets and Product Literature