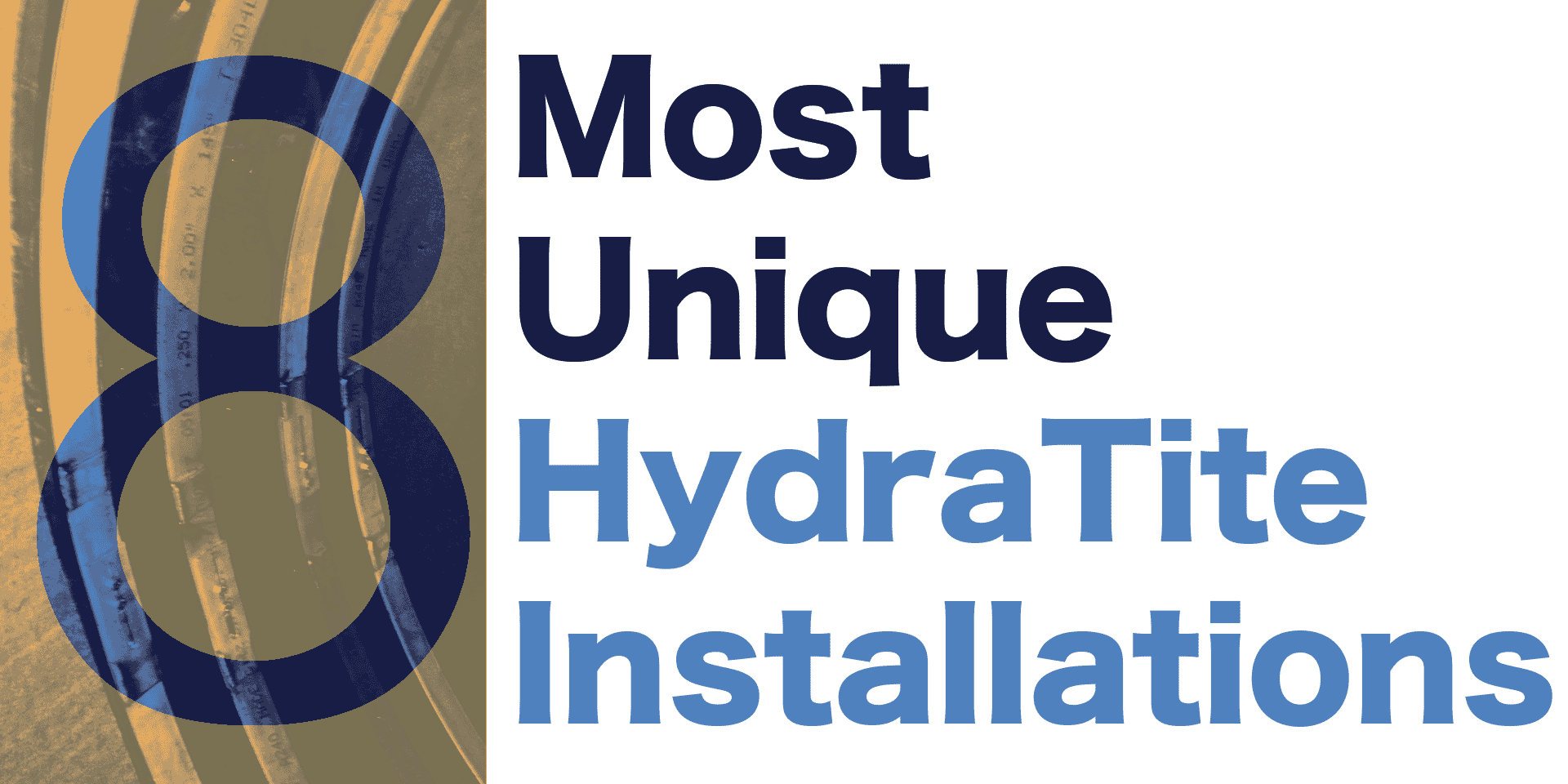
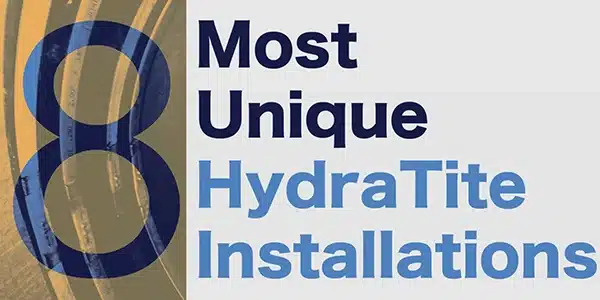
In HydraTite’s 25-plus years of use, it has been installed in many interesting and unusual projects. These range from installations in culverts amid freezing cold water to those in both pipes so large they require scaffolding and pipes nearly too small for a person to enter. Some projects required over a thousand seals, while others needed custom seals manufactured for oddly shaped pipes. Many projects require HydraTite installation despite some standing water, but some projects required seals installed completely underwater. Finally, HydraTite is a joint or point repair, but it can also be interlocked to protect an extended section of pipe if needed and in some projects, it has been interlocked many times. Let’s revisit the eight most memorable projects from the last decade demonstrating the versatility of HydraTite.
1
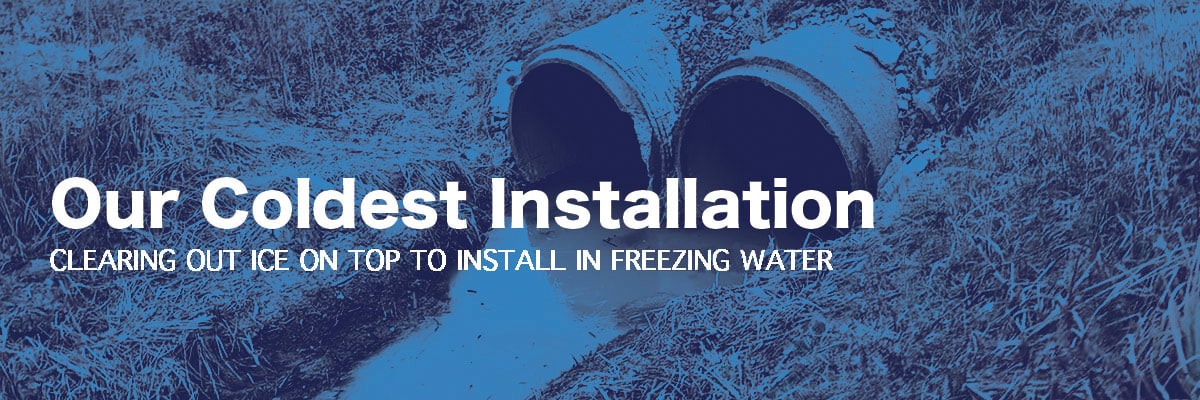
2020
This culvert had been repaired multiple times. Multiple joints had two different types of grout in them, both now failing. The Field Service crew had to bundle up in preparation for the installation as they had to break a surface layer of ice before they could begin. HydraTite of varying widths (11”-21”) was installed, and some of these seals were reinforced with stainless steel backing plates where the joint’s separation was more severe. As the seals were installed the Field Service members would occasionally leave the pipe to retrieve supplies and would have to rebreak the ice when they returned.
In only three days, HydraTech had to grind and clean the concrete surface of the culvert and install 31 seals, many with backing plates. HydraTech beat this deadline and completed the project in only 2 days.
There is an entire blog post devoted to this project under resources, where you can also find a related video on this case study.
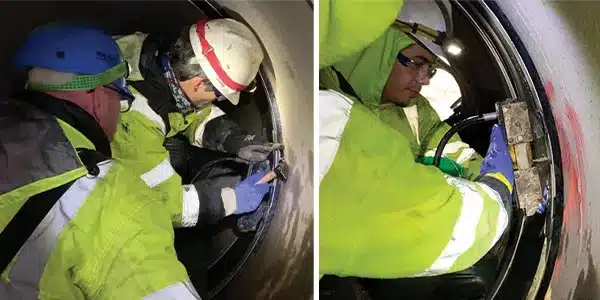
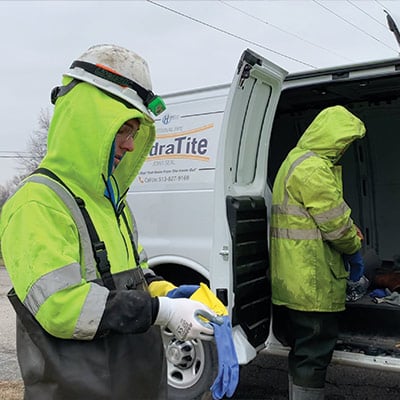
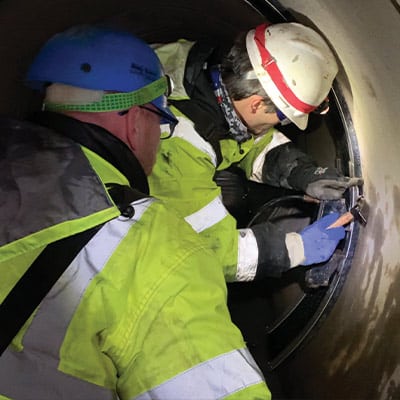
2
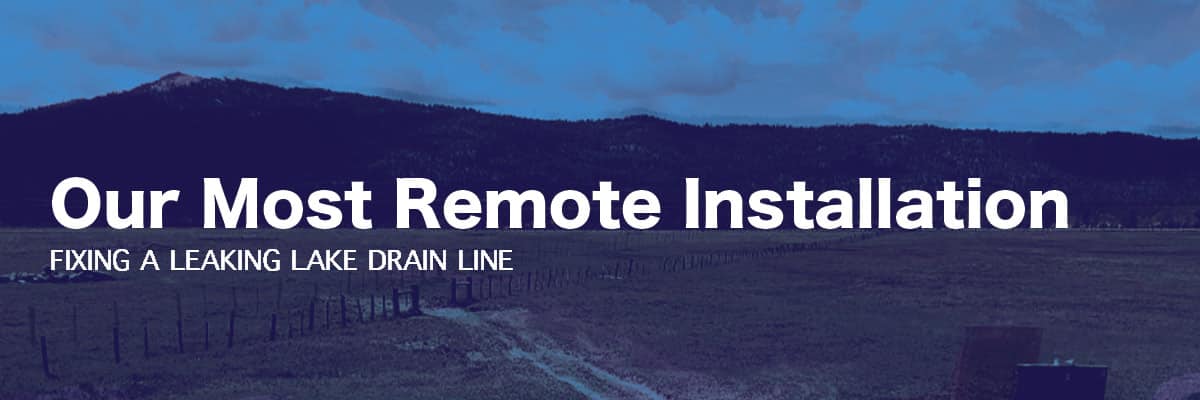
2019
A leaking irrigation pipe on a ranch in Idaho needed rapid repair. For the sake of the bison that relied on this pipe for water, a rapid solution was necessary. However, to get to the pipe, the Field Service technicians had to drive miles off of the road.
Custom band size and multi-piece configurations were engineered and manufactured for this project. The seal installation was to be completed beyond and around the 45-degree bend. HydraTite repaired the irrigation system for a lower cost than other repair methods, and the project was completed in only a few days.
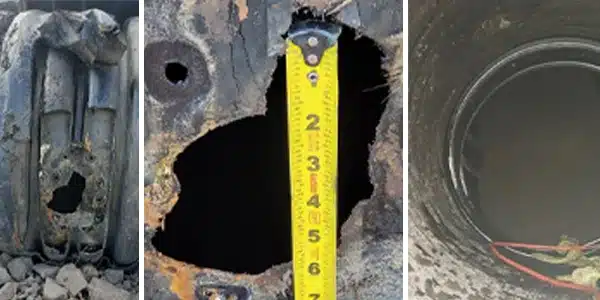
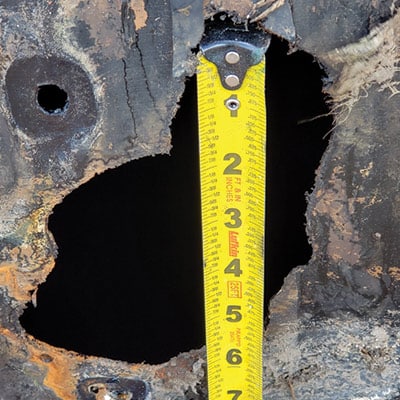
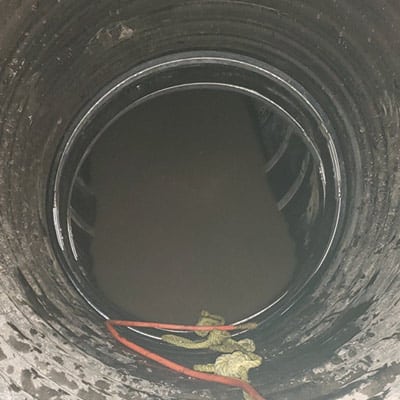
3
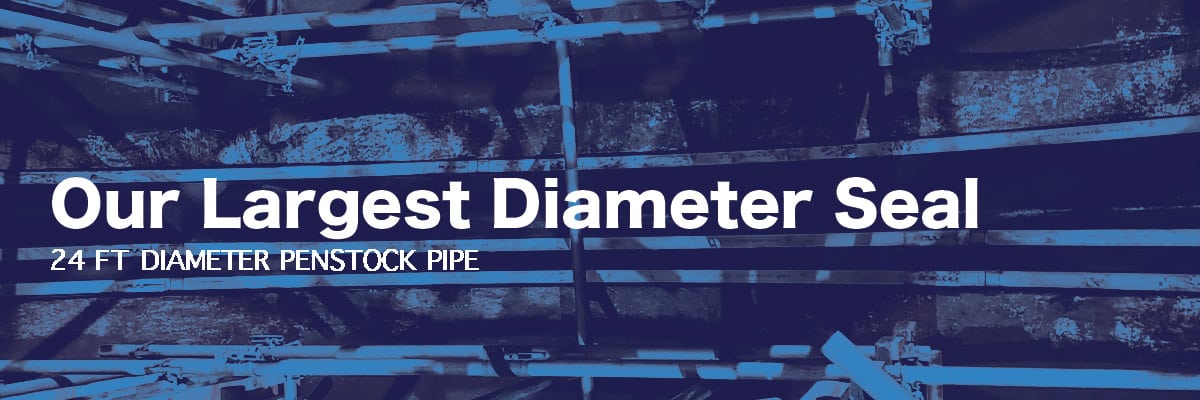
2020
Previously the largest diameter pipe in which HydraTite had been installed was an 18-foot diameter pipe. Then HydraTech oversaw installation in a 24-foot diameter pipe, which required the construction of a two-story scaffolding and the use of rubber and cement fillers to make a flush surface for the seal. This Canadian project required two HydraTite seals to protect deteriorated joints, and HydraTite was able to do so despite the slope sections near the joints. The pipe was already shut down for other repairs and the task was completed in this window, meaning the HydraTite installation required no additional downtime.
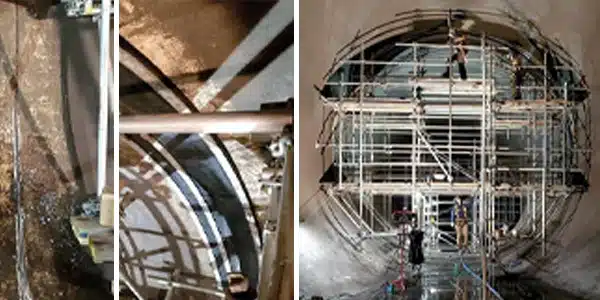
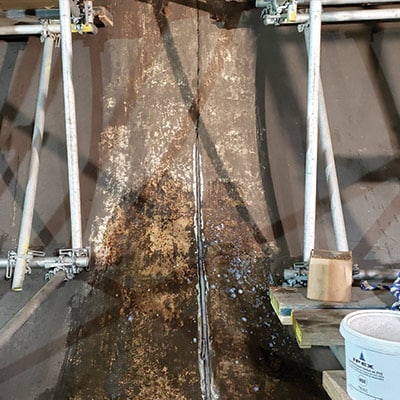
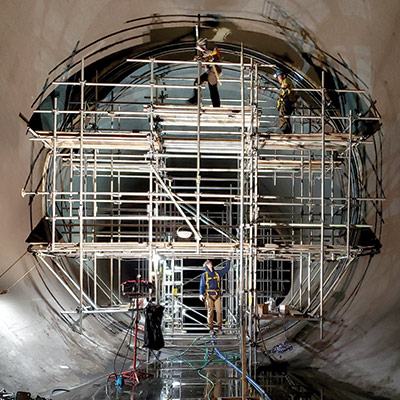
4
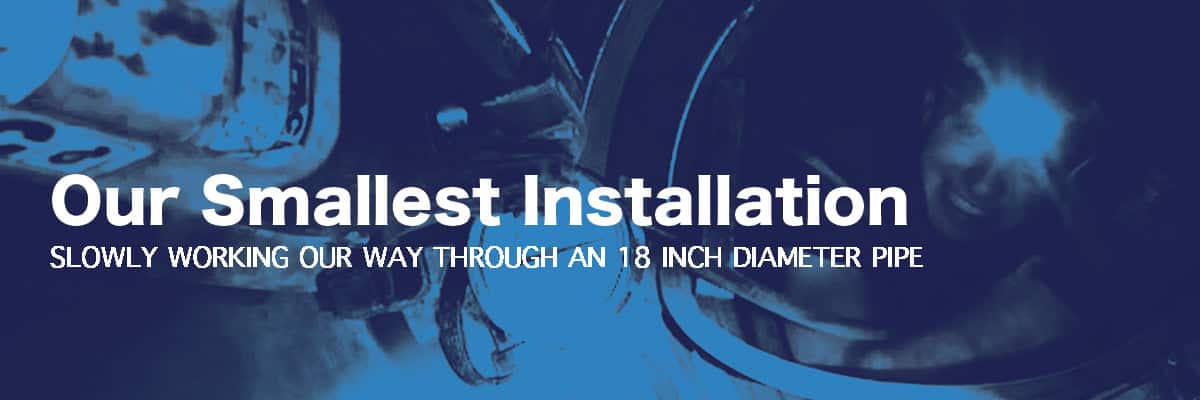
2018
The inner workings of this city water fountain had begun to leak and each of its joints required repair. The farther in our Field Service technicians went, the smaller and smaller in diameter the pipe became. The largest in diameter HydraTite seal installed was 24″ and the smallest was 18″. The technicians had to wiggle their way into the pipe on top of a small riding cart. Since the pipe was not big enough to facilitate a turn around they had to slowly wiggle their way back out hundreds of feet. HydraTite was installed rapidly, and the fountain was soon turned back on.
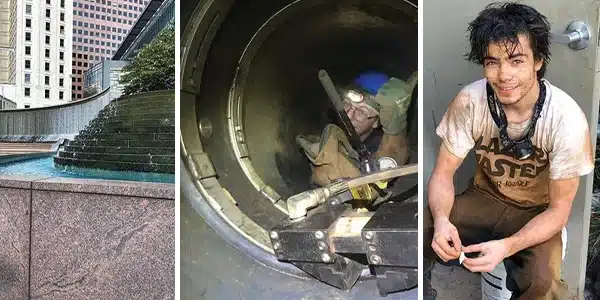
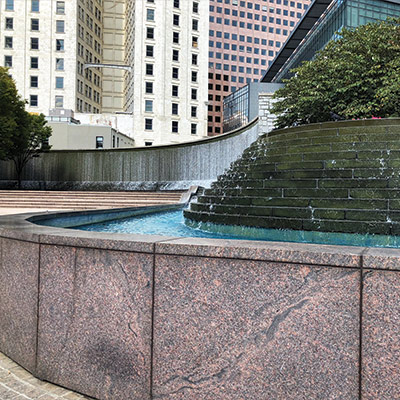
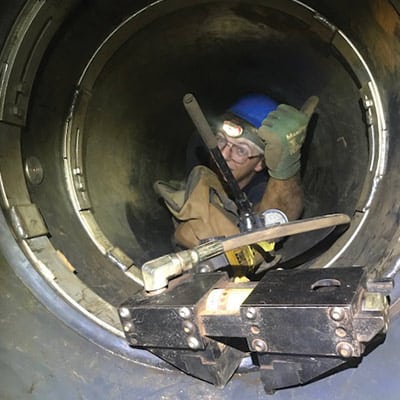
5
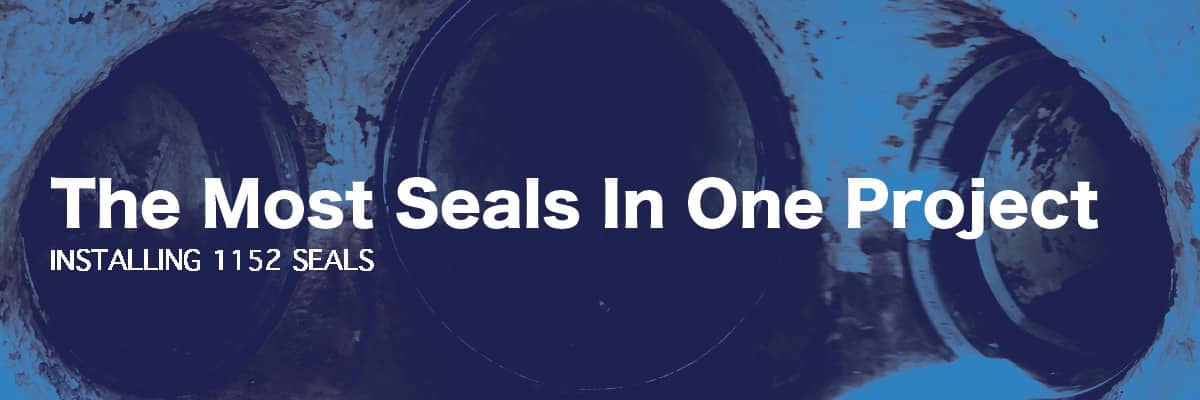
2019
The aging cast iron water main’s deteriorating joints were threatening water quality and exfiltration. Previous repair methods had been employed, but they had begun failing. A trenchless solution was required as replacing the pipe would disturb the above museums, galleries, and other facilities. Seals of various diameters were required for this project, but most of the seals were 30″ and 36″ in diameter. Multiple unused service taps and abandoned connections had to be blocked off or covered with the seal as well.
1152 HydraTite seals eliminated the exfiltration at all of the joints without disturbing the buildings above. The repair also ensured that the water main pipe’s future operation would be more cost-effective.
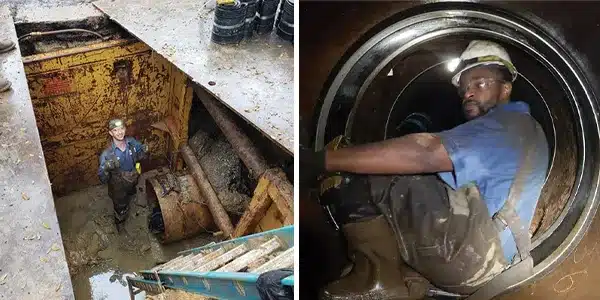
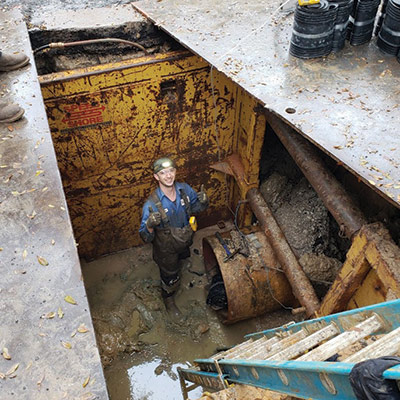
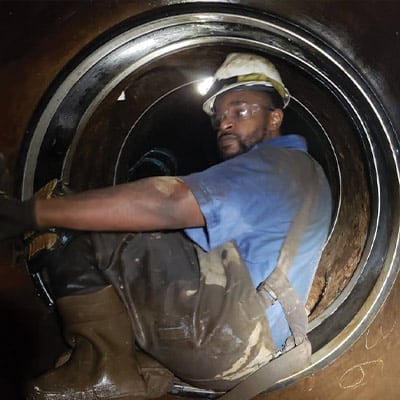
6
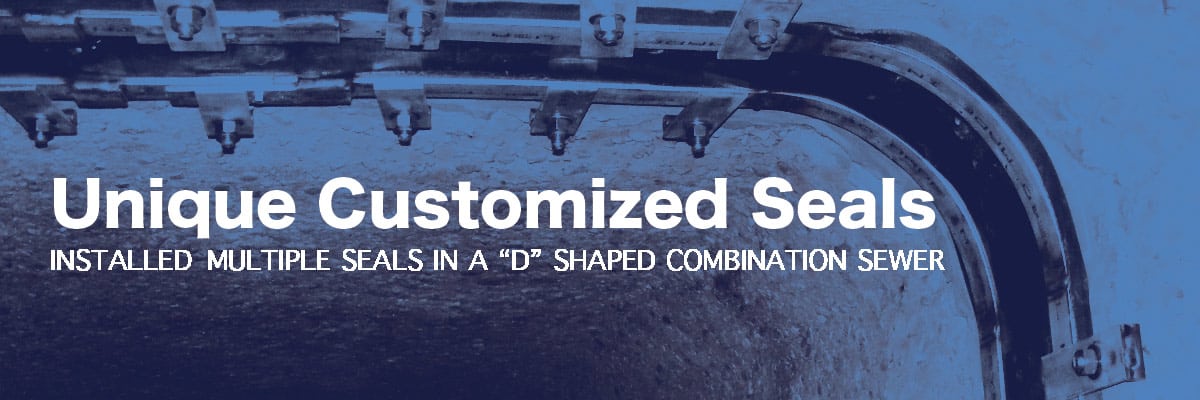
2012
32 joints in this elevated trestle pipe were deteriorating and leaks were forming. The interior surface of the pipe was slowly facing degradation by biological corrosion. A solution was needed to ensure that the contents of this sewer line did not escape the pipe, but the irregular shape of the pipe meant that HydraTech couldn’t just use a standard seal. Up until this point, the HydraTite seal had only been installed in circular and elliptical pipes. Despite this, a custom seal was engineered and manufactured to fit the odd shape.
Hydraulic cement was used to mend the deteriorated surface so that the seals could be installed properly. The 32 seals were installed and tested at a fraction of the time and cost that other more traditional repair and replacement methods would have required. HydraTite has continued to protect the pipe for nearly a decade and will continue to protect it for many years to come.
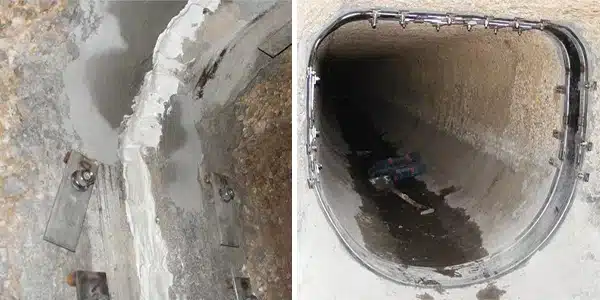
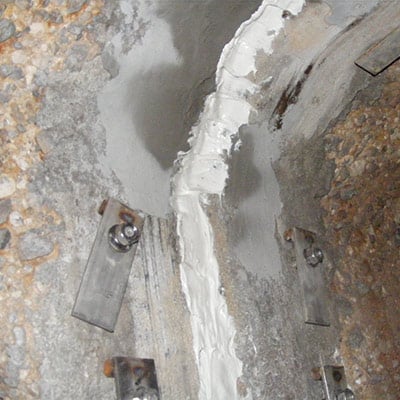
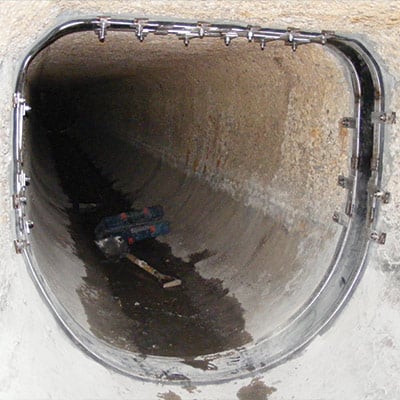
7
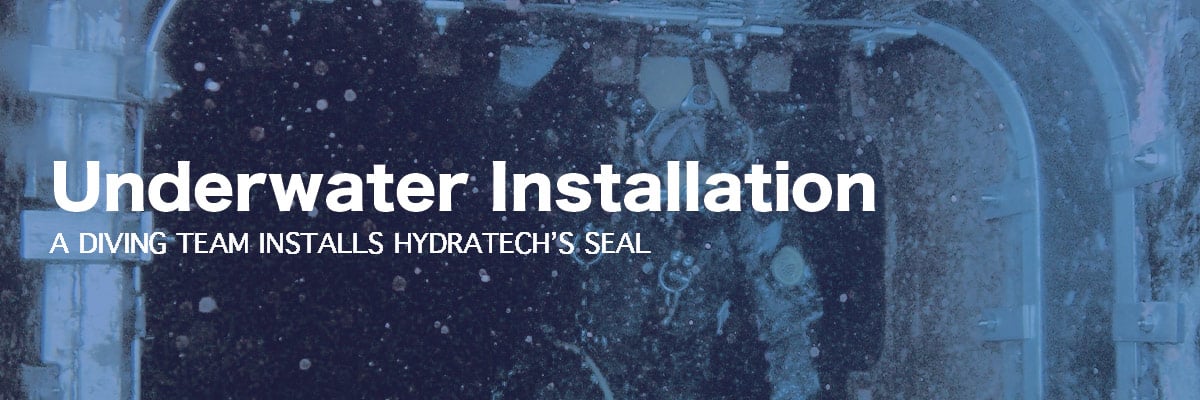
2017
This project included three custom box seals that were 54″ in height by 54″ in width, of which two were double wide and one was extra wide. It is not uncommon that HydraTite is installed with some water in the pipe, but these seals were installed and even tested completely underwater. The test was completed by applying a dye near the edge of the seal to see if any worked its way under the seal. As shown in the accompanying animation, there was no leak, and HydraTite proved effective even underwater for an unusual shape.
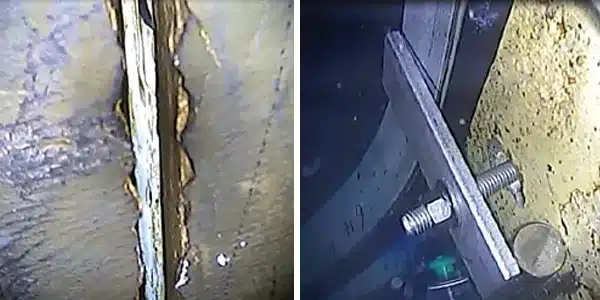
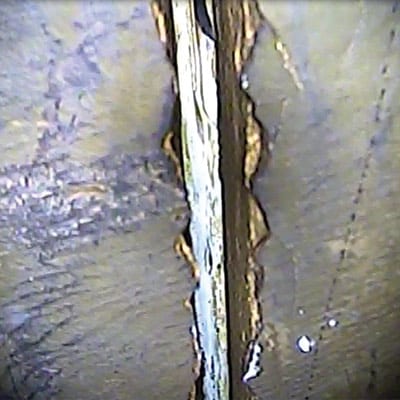
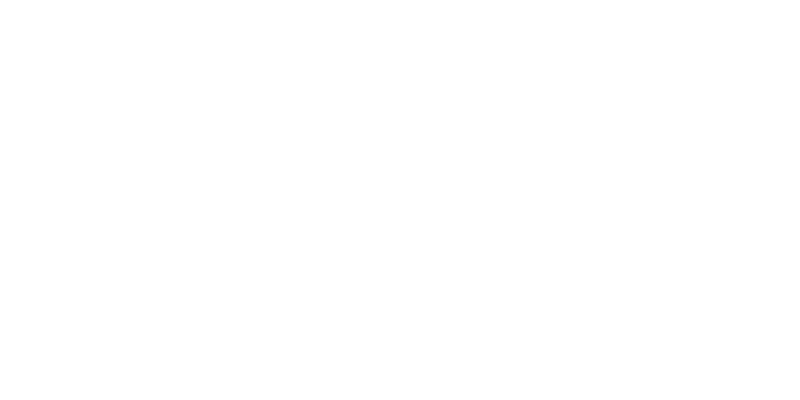
8
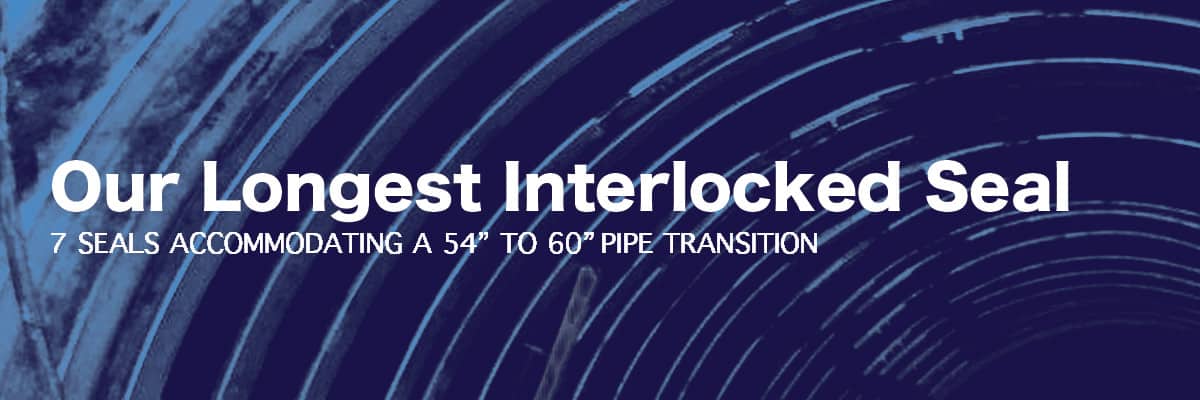
2019
A sewer line beneath a scenic canyon in Southern California was deteriorating, and joints along miles of pipe needed to be repaired quickly. The sections of pipe were connected end to end with interior liners fused using weld strips. Many of these strips were loosening and falling out only to be found downstream and in manholes. A trenchless solution was preferable to protect the surrounding environment from digging, and a solution was needed quickly to ensure that the sewer line did not leak and harm the river wildlife as well.
This job required over 1,000 HydraTite seals, while it was nearly a job with the most seals installed, the reason this job made the list was one unique joint. This joint was between pipes of different diameters. A 54″ pipe was attached to a 60″ pipe, and this joint required more than just a large seal. Seven seals had to be interlocked to ensure that the transition between pipes would be watertight. This project was unique in that the design required increasing diameters in an interlocking application. Accurate engineering and manufacturing made this installation a watertight success.
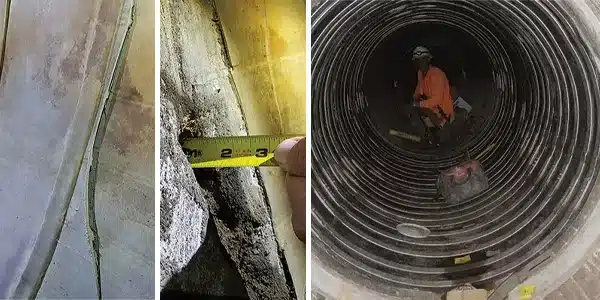
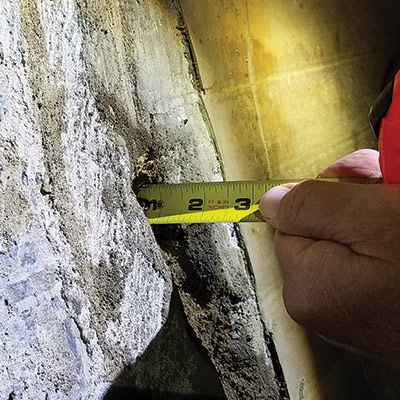
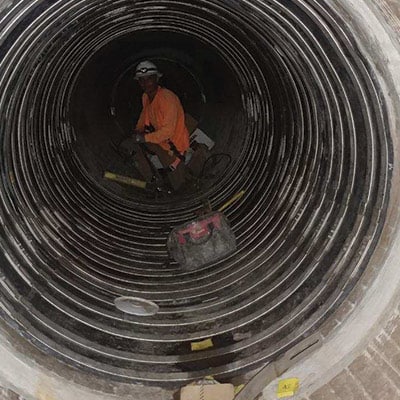